3232853 - 1080B exhaust emission control system
The electronic control unit identifies the composition of the mixture (rich or lean) from the Lambda sensor output voltage.It adjusts the quantity of fuel injected to ensure the optimum composition of the mixture (l = 1) to create the ideal conditions for the treatment of the exhaust gases in the catalytic converter.If the mixture is too rich (lambda less than 1), then the quantity of fuel should be reduced and, if the mixture is too lean (lambda greater than 1), then the quantity of fuel should be increased.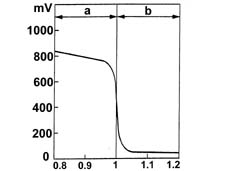
CONSTRUCTION FEATURES
Lambda sensors
Both lambda sensors upstream of the catalytic converters are linear, while the downstream sensors are planar and inform the control unit about the progress of combustion (stoichiometric ratio).The upstream sensors (? 0.7 2.0) carry out the check on the mixture strength (except during idling) known as the 1st loop (upstream sensors closed loop).The sensors downstream of the catalyzer are used for the catalyzer diagnosis and for finely modulating the 1st loop control parameters.With this in mind, the adjustment of the second loop is designed to recover both production differences and those in the response of the upstream sensors which may occur as a result of ageing and pollution.This control is known as the 2nd loop (downstream sensors closed loop).The electronic control unit identifies the composition of the mixture (rich or lean) from the Lambda sensor output voltage.It adjusts the quantity of fuel injected to ensure the optimum composition of the mixture (? = 1) to create the ideal conditions for the treatment of the exhaust gases in the catalytic converter.If the mixture is too rich (? < 1), then the quantity of fuel should be reduced and, if the mixture is too lean (? > 1), then the quantity of fuel should be increased.Planar Lambda sensors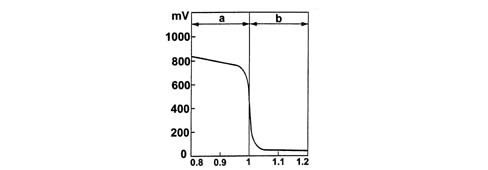
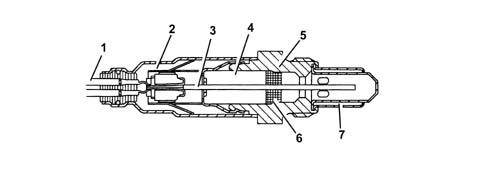
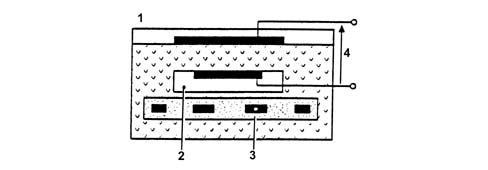
Catalytic converter
The three-way catalytic converter simultaneously reduces the three polluting gases present in the exhaust gases:
- unburnt hydrocarbons (HC);
- carbon monoxide (CO);
- nitrogen oxides (NOx).
Two types of chemical reactions take place in the converter:
- oxidation of the CO and HC, converted into carbon dioxide (CO2) and water (H2O)
- reduction of the NOx converted into nitrogen (N2).
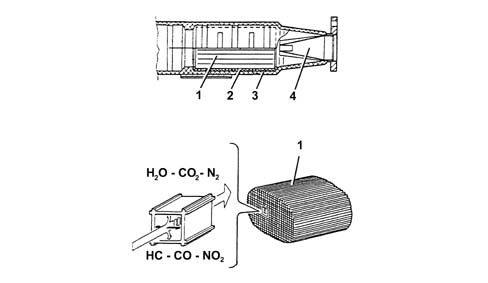
![]() | The noble metals contained in the catalytic converter, because of the high temperature, are chemically attacked if lead is present. For this reason the use of petrols containing lead should be avoided, otherwise the converter will be quickly and irreversibly damaged. Never use petrol containing lead, not even in an emergency or for a very short time. |