2401118 - Introduction - PANELS AND FRAME
Introduction
The subjects have been developed, documenting, above all, the technical innovations, useful for overcoming the various tests set by the new legislation, assisting the description and teaching aspects, limited to providing minimal ideas, rules and precautions. For information on repair techniques and vehicle technical data, refer to the descriptions in the specific sections in the Repair Manual.Aerodynamics
The style of the new vehicle, featuring an extremely personalized and original design, has concentrated on developing the high levels of versatility, comfort, functionality and strength already achieved with previous models. The front section, the side panels with glazed areas, the joined surfaces, the rear section and the underbody have all been designed with special attention paid to the aerodynamic profile and have made it possible to achieve the following results: The following values are given as an example:Basic trim level version:
- drag coefficient Cd = 0.32
- area drag coefficient CD x S = 0.7574
Safety
The main aim of car manufacturers is undoubtedly the complete safety of the driver and passengers. To adapt the vehicle to market regulations, both European and world wide, which have become very exacting, the new vehicle has been designed with care taken over every detail in order to respond in the best possible way to all situations.Specifications
The high torsion and bending strength of the vehicle, in addition to endowing the vehicle with excellent passive resistance properties, also translates into manifold advantages:
- less noise thanks to fewer vibrations;
- no creaking from the trims;
- improved driveability, keeping the suspension angles correct; extremely precise driving with a sensation of a firm ride and great comfort;
- – increased resistance to failure caused by the use of the vehicle over particularly uneven roads;
- the sensation of a compact car;
- maintenance in time of the overall qualities of the vehicle.
Torsional rigidity
Torsion deformation diagram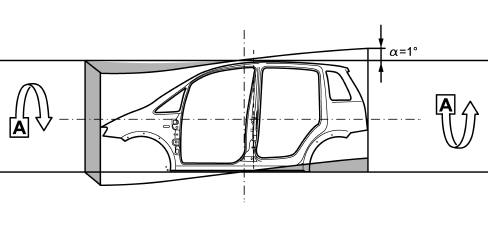
Torsional rigidity
Torsional strength valuesBody with bonded windscreen: 1290 kgm/mmBending strength
Bending deformation diagram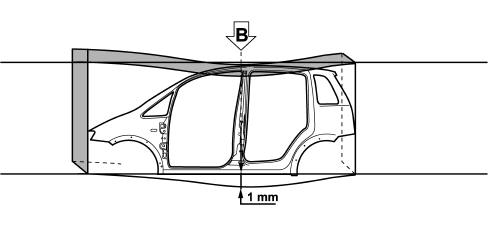
Bending strength
Bending strength valuesBody with bonded windscreen: 755 kgm/mmPreventative safety
This involves all those factors which determine the comfort of driving conditions and allow situations which could distract the attention of the driver to be prevented:
- extremely rigid bodyshell for greater driving safety;
- optimum engine mountings (barycentric type) to keep transmission of vibrations and noise to a minimum;
- climate control system (if applicable), fitted with a pollen filter, with balanced distribution throughout the passenger compartment which, thanks to the arrangement of the vents, allows an excellent exchange of air and comfort;
- optimum visibility conditions thanks to the extensive glazed area;
- specially shaped rear light clusters which give optimum light and signalling functions;
- the layout of the steering wheel (optionally height-adjustable), the pedals, the main controls and the warning lights has been carefully thought out to obtain a good balance between the driving position and the ease of reaching these controls;
- height adjustable steering wheel (where applicable) allowing the ideal driving position to be found;
- generous dimensions of the interior spaces allow the necessary comfort for the occupants of the vehicle;
- abundant use of sound insulation materials and the adoption of special solutions for anti-vibration fixings to lower the mechanical noise and ensure quiet driving;
- interior fittings which conform to the most stringent regulations governing flammability.
Active safety
This is represented by the features of the vehicle and the specific components which allow critical moments when driving the vehicle to be overcomeThe following contribute to the active safety of the vehicle:
- excellent driving stability and dynamic handling of the vehicle;
- excellent braking system;
- good acceleration.
In this field, the vehicle adopts solutions which include:
- front suspension which guarantees good control both for normal and sports driving, allowing precise driving and control of the vehicle, even in the wet and on surfaces with poor grip, an immediate and precise response and a capacity to absorb obstacles and uneven road conditions;
- torsion beam rear suspension designed to offer better handling performance. The torsion beam ensures ideal suspension torsional rigidity for an excellent balance between car front and rear;
- smart bushes attach the rear axle to the body. These allow minimal self-steering modulated by bush stiffness;
- new design electric steering (where fitted) designed to allow a precise, immediate response in all situations;
- braking system, designed to ensure braking power and safety free from fading, consisting of two independent crossover circuits. an ABS/EBD system, which is the most advanced braking control system currently available with 4 channels and 4 active sensors which reduce the implementation times and an E.B.D. device (Electronic Brake Force Distribution) which makes it possible to dispense with the load proportioning valve.
- integral traction control device ESP with ESP/ASR/HHC functions (where applicable).
Passive safety
Since, statistically, above 60% of accidents involve frontal impacts, 30% side impacts and the remaining 10% include bumps, fires and overturning, the structure of the vehicle has been designed and developed with crumple zones which absorb the energy developed during an impact without affecting the survival space inside the passenger compartment. The seat and seat belt mountings have been reinforced in order to protect the occupants of the vehicle (three branch available for the centre rear seat).There is a dual stage protection system, fitted as standard, for the occupants of the front seats which includes a driver's Air Bag, seat belt pretensioners with load limiters, a passenger Air Bag (which can be manually disabled using the ignition key in aa barrel in the right dashboard panel), a decentralized additional frontal impact detection sensor located near the bonnet lock which assists the main electronic control unit to anticipate the intervention of the Air Bags compared with the conventional system cancelling the risk of minor injury resulting from the activation of the Air Bags, in addition to the optional extras available for the vehicle such as Side Bags for the driver and front passenger and Head Bags which extend under the roof along the left and right sides protecting the occupant's heads from any side impacts.The model is also equipped with ISOFIX attachments at the rear seats for transporting the smallest passengers in safety.![]() | In the case of operations to the bodyshell, if the structural reinforcements are distorted they must always be replaced. |
General characteristics
The differentiated strength bodyshell has strengthening reinforcements for the survival chamber to resist frontal impacts to ensure the indestructibility of the passenger compartment, offering maximum protection for the occupants and keeping the effect of the impact to a minimum.The following are the main operations which have been carried out to the bodyshell to achieve the proposed objectives:
- differentiated strength front structure with reinforcements in the struts, designed to crumple in a pre-set fashion absorbing and distributing the force of the impact to the structure thanks to the connecting front crossmember which also allows non central impacts to be absorbed.
- reinforcements in the side members and the side pillars connected by a box section crossmember under the windscreen which ensures the transverse rigidity of the passenger compartment joining the side panels at waist height;
- reinforcements under the floor panel, which increase the solidness and the strength of the floor, limiting deformations as far as possible;
- adoption of bonnet lid retaining hooks and telescopic, collapsible steering column.
Components
.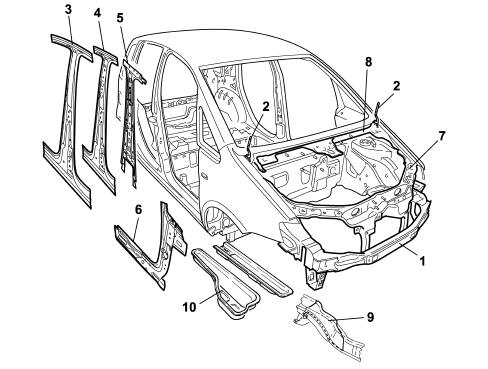
General characteristics
As far as resistance to side impacts is concerned, the bodyshell has been designed to conform to the most recent European regulations and is capable of guaranteeing a high level of safety with special crumple zones in the case of an impact which ensure the passenger survival cell protecting the occupants.The above has been achieved by:
- reinforcing the side members under the door between the front pillars and the centre pillars;
- reinforcing the centre and rear pillars at the attachment points to the side members, the anchorage points of the seat belts and the areas of the lock strikers;
- inserting a box section einforcement crossmember between the underdoor side members.
Components
.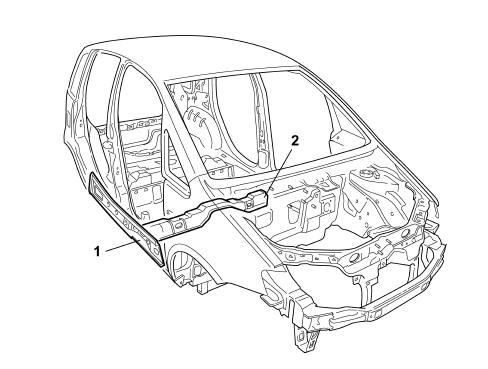
General characteristics
The structure of the doors is of fundamental importance for the safety of the passengers in the case of side impacts, and has therefore been designed with optimum geometry and rigidity of the door panels to complete the capacity to maintain the survival cell and keep possible injury of the occupants to a minimum. The door structure is supported by a carrier that holds all components such as electric windows, door catches, internal door opening handle speaker in place so the door can be opened after the front and rear impact tests required by the law.This has been achieved by:
- adopting tubular impact beams and waist reinforcements along the line of the pillars, so completiing an ideal high-strength door surround;
- adopting high resistance locks and strikers;
- using energy absorption internal door liners with no sharp edges, designed to ensure the minimum impact with the occupant in the case of an accident;
Components
.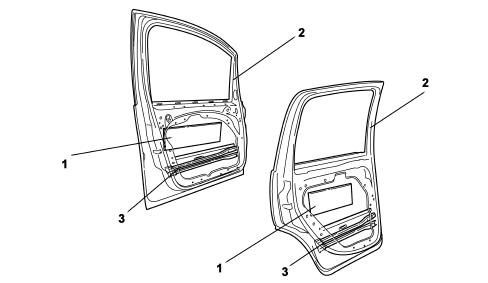
General characteristics
The particular structure of the roof confers greater strength on the passenger compartment contributing to the safety of the passengers both in the case of a side impact or if the vehicle overturns which, although only involving a small percentage of accidents, is one of the most dangerous types.The following increase the solidity of the structure of the passenger compartment:
- transverse connecting box sections between the side panels by the top part of the windscreen and the tailgate;
- structural adhesive sections along the edges of the upper windscreen and tailgate compartment box sections.
Components
.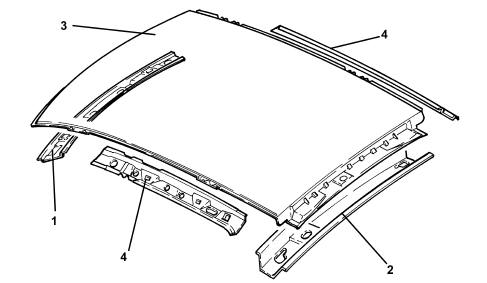
General characteristics
The resistance to rear impacts is very high and exceeds the tests established by the most stringent European regulations.This is ensured by:
- reinforced rear box section crossmember;
- reinforcements in the attachments between the rear crossmember and the pillars;
- tailgate with reinforced frame;
- reinforced rear wheel arch liners and side frame.
Components
.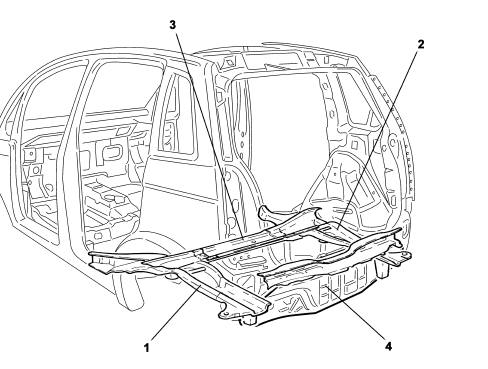
WINDSCREEN AND WINDOWS
A further contribution to safety is provided by the fixed windows.A stratified windscreen has been adopted to increase the safety of the vehicle. This solution means that if the windscreen is affected by stonechipping or is hit by an object and shatters, visibility is maintained and a high degree of protection is offered in the case of impact with the head. The windscreen is bonded to the bodyshell, thereby increasing the structural rigidity of the vehicle: the seal contributes greatly in reducing wind noise.Protection against fire
This is achieved through the FPS (Fire Prevention System) which consists of:
- fire-retardant interiors, all covers satisfy the most stringent USA regulations on flammability; in fact, they do not ignite in the case of occasional contact with heat sources (e.g. a cigarette) and limit the propagation speed of the flame;
- inertia switch for cutting off the fuel pump;
- antimisfiring shields (overheating of the catalyzer, for petrol versions) which insulate the catalytic silencer and protect the braking system and fuel pipes;
- electrical equipment protected by maxi fuses which guarantee a break in the supply in the case of a short circuit or overheating which could occur in the case of a fire;
- battery retention in the case of an impact or overturning;
- cut-off valve which eliminates fuel leaks if the car rolls over;
- fuel tank made from a plastic material which has high mechanical and fire resistance properties, firmly secured to the bodyshell in a protected position
- layout of the electrical equipment, the fuel pipes and the braking system pipes designed to keep the risk of fire in the case of an accident or failure to a minimum.
GENERAL CHARACTERISTICS
In order to meet EEC regulations the design of the car has produced exterior noise levels below 74 decibels.Driving comfort and quality of life inside the car have been improved by:
- optimizing the bodyshell with the careful design of all components subject to noise, where the rigidity has been increased and the fixings have been reinforced.
- selecting the contact materials with great care;
- working on the insulation of noise transmitted from the road surface, the mechanics, the suspension;
- taking care of the assembly of the parts, the aerodynamics and all those components which, with their inevitable profiles, often adversely affect acoustic comfort, such as the door handles, external rear view mirrors, bumpers, various profiles;
- adopting new generation engine types with technological contents also designed to improve acoustic/vibrational aspects;
- by adopting a new barycentric engine mounting system.
A further area of intervention has been the insulation of the passenger compartment involving:
- highly efficient sound absorbing materials which are excellent both in terms of thickness and their layout on the vehicle;
- fitting a sound-absorbent shield in the lower part of the engine bay to insulate it acoustically.
- the elimination of acoustic holes, i.e. areas where noise passes between the engine compartment and the passenger compartment which has been achieved by using double seals and thicker rubber plugs;
- coupling between various sound insulation elements with restricted tolerance to avoid uncovered sections;
- the extensive use of sound absorbing material seals;
- sound insulation linings for the panels with thermo-bonding materials applied before painting;
- linings for the partition and the front running boards to eliminate the sensation of the engine;
- the application, before painting, of thermo-expandable materials inside the box sections to reduce the transmission of noise; During bodyshell cataphoresis, these materials increase in volume by around ten times thereby completely filling the box section;
- appropriately lining the luggage compartment to reduce rolling noise;
- carefully studying the couplings and the dimensions of the parts subject to creaking, for example the dashboard, heater and seats where the mountings and couplings have been reinforced.
![]() | To maintain the high level of acoustic comfort reached, in the case of repairs, the solutions adopted during construction must be restored exactly. |
Diagram showing application of thermo-bonding materials on the vehicle
.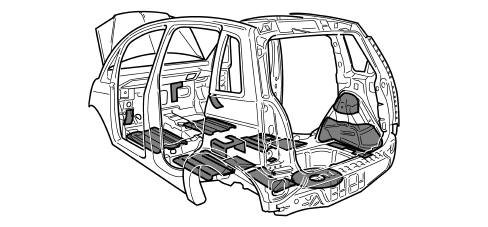
Introduction
The bodyshell of the vehicle has been designed to be resistant for many years (8 years for perforation, 10 years for structural weakening) to any kind of environmental attacks as far as both the internal parts, which are not visible but potentially subject to corrosion, and the external parts, subject above all to damage which could adversely affect the appearance of the vehicle, are concerned. These results have been achieved by studying the structure of the internal panels to minimize exposure to corrosive penetration, making widespread use of galvanized panels and using multiple protective treatments on all the inner and outer panel surfaces.Galvanizing
Galvanized panels can be produced through two different technological processes:
- galvanizing process deposition: the panel comes into contact with if one side only is involved (SINGLE-GALVANIZED PANEL) or is immersed if both sides are treated (DOUBLE-GALVANIZED PANELS) a solution of zinc salts which deposits a layer of pure zinc with a high degree of surface finish through the electrolytic effect;
- in the case of high temperature deposition, molten zinc is deposited on the panel by the effect of heat. This process, which is used mainly for structural elements of the bodyshell, can produce zinc thicknesses of up to 20 micron to be used for the parts most exposed to corrosion, compared with the 8 micron normally used for the rest of the galvanized panels.
86% of the vehicle bodyshell is made from galvanized panels divided as follows:
- ~ 70% double layer galvanized panels 7.5 m
- ~ 7% double layer galvanized panels 20 m
- ~ 9% single layer galvanized panels 7.5 m (electro-galvanized)
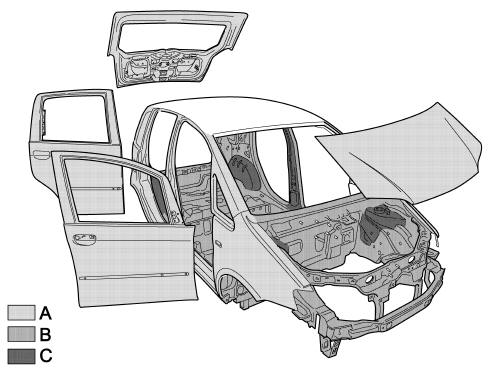
Galvanizing
A Double galvanized panels 7.5 micronB Single galvanized panels 7.5 micron C 20 micron double galvanized panels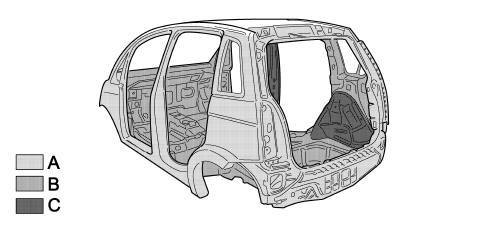
Galvanizing
A Double galvanized panels 7.5 micronB Single galvanized panels 7.5 micron C 20 micron double galvanised panelsSpecifications
The vehicle colour range includes pastel shades (two-layer); metallic colours.The type of colour for the vehicle and its characteristics are indicated on the identification plate which contains the following information: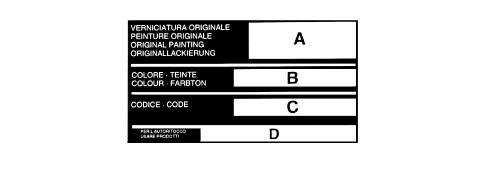
Components
The aim of painting the bodyshell is:
- to protect the panels from corrosion due to exposure to atmospheric conditions;
- to reach and maintain high levels of shine and fullness of colour, over a period of time.
![]() | During servicing operations which involve replacing box sections, the wax based oil treatment must be renewed. |
MAIN SPECIFICATIONS
According to the EEC End Of Life (EOL) directive, a total of 80% of metal and non-metallic parts should be recovered to produce new material and 5% of the remainder should be used for energy production. At present, some 75% of the vehicle consists of metal that can be easily recovered for smelting by using the different metal melting points. All the remaining parts of the vehicle, i.e. some 25% by weight, must be recovered prior to this stage. The problem of recycling plastic materials can be solved from the design; during this stage is it necessary to evaluate the possiblity of resusing the material in future components.The aims to be considered during design include:
- ease of component disassembly;
- choice of noble materials in the recyclable polymer chain (with priority given to parts made out of a single family, e.g. PP).
The plastic materials are recycled in a cascade pattern. For example:
- insulating materials for building are obtained from seat upholstery;
- the material for wheel arch liners which comes from the bumpers is then used in the next stage for producing sound insulation linings and finally ends up as fuel for the production of energy.
Diagram showing reuse of recycled materials
.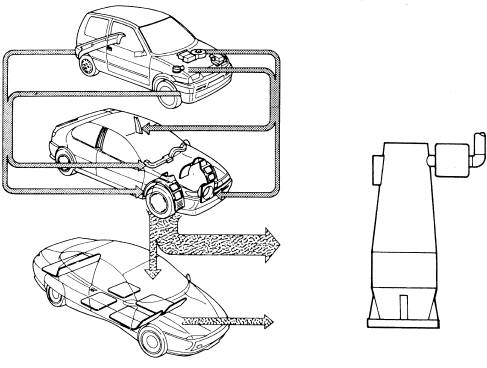
Marking a proportion of recycled material
.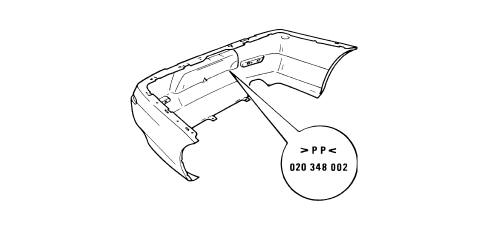
Car parts where the recycling flow is active
.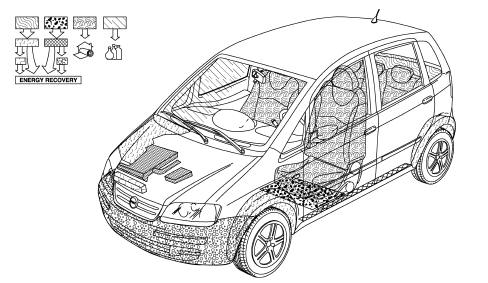
MEASUREMENTS FOR ADJUSTING MOVEABLE PARTS
In order to facilitate and check the operations of dismantling the moveable parts, here is a list of the existing openings (measurements expressed in millimetres) for appropriate adjustments. The adjustment methods are illustrated in the sections containing the procedures for removing and refitting the moveable parts.View of 5 door car (front 3/4) showing position of points where gaps between moveable parts are measured.
.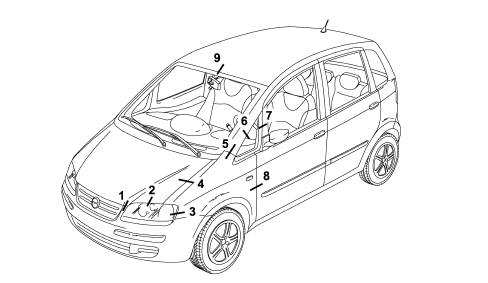
Measuring points for gaps between parts 1 to 6.
.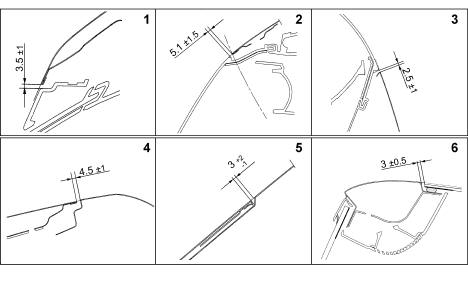
Measuring points for gaps between parts 7 to 9
.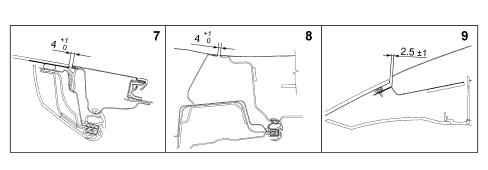
Measuring points for gaps between parts 10 to 15
.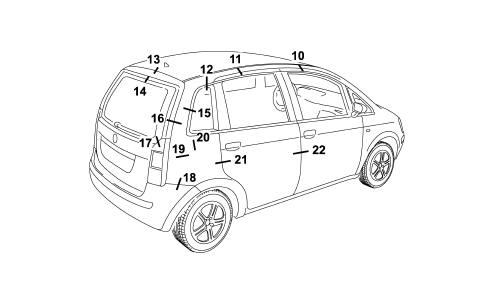
View of 5 door car (rear 3/4) showing position of points where gaps between moveable parts are measured.
.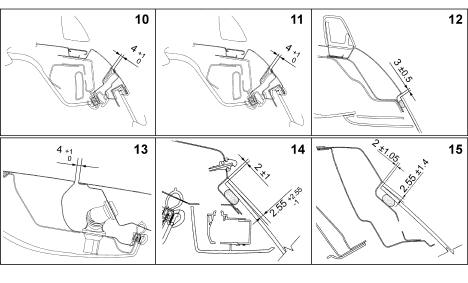
Measuring points for gaps between parts 16 to 22
.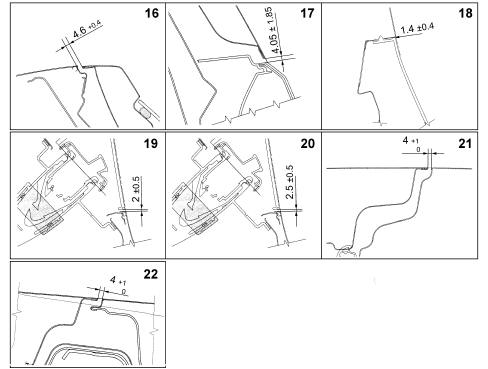
Front view of car showing sealant application areas
.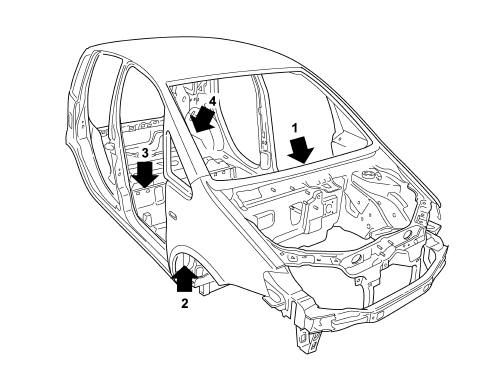
Rear view of car showing sealant application areas.
.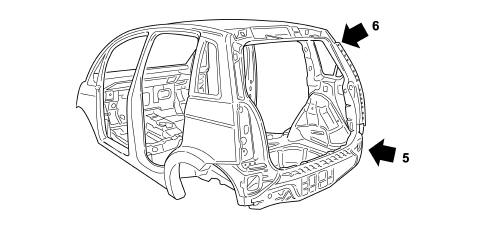
Detail showing application of sealant to zones 1 to 3
.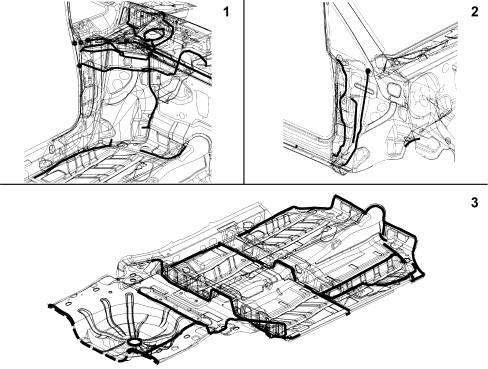
Detail showing application of sealant to zones 4 to 6
.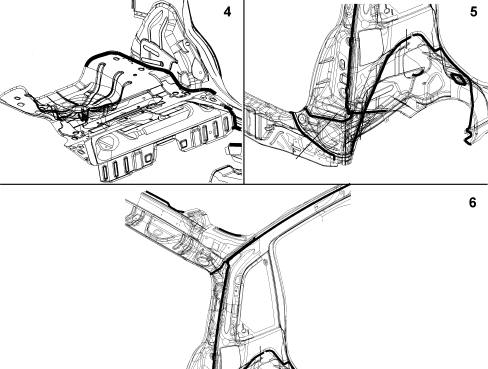
DIAGRAM FOR CHECKING UNDERBODY
This chapter contains typical body measurements that may be used by bodyshops to achieve the best results if repairs are necessary. The comparative dimensions, expressed in millimetres, may vary slightly (by about 2 mm). Experienced repairers will be able to establish whether differences are due to impact or manufacturing tolerances.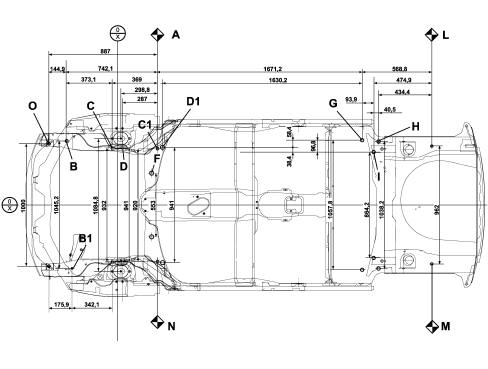